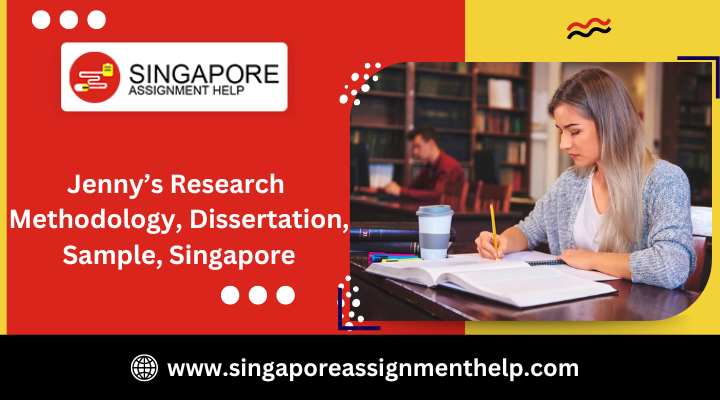
Jenny’s Research Methodology, Dissertation Sample Singapore
The blade outlet angle, wrap angle, and blade count of an automotive coolant pump impeller were optimized to enhance efficiency while maintaining size. Three new designs were tested, and the best was compared to the original. Experiments confirmed that the optimized impeller’s energy characteristics closely matched experimental data. Analysis revealed that increasing the wrap angle and reducing the blade outlet angle improved flow conditions and pressure distribution, especially at low flow rates. At the designed flow rate, this also significantly increased pump efficiency. The optimized impeller achieved a maximum efficiency increase of 4.8%, guiding future pump design to reduce automotive cooling system energy consumption.
Hire a Professional Essay & Assignment Writer for completing your Academic Assessments
Native Singapore Writers Team
- 100% Plagiarism-Free Essay
- Highest Satisfaction Rate
- Free Revision
- On-Time Delivery
Introduction
The automotive coolant pump is crucial for engine cooling, circulating coolant through piping to ensure engine operation. Limited installation space restricts the impeller’s radial distance, necessitating high rotational speeds. Consequently, the pump must also cool its drive motor, requiring a complex flow channel to direct coolant to the rotor and back. Automotive coolant pumps are smaller and have more complex runners than standard centrifugal pumps, often resulting in lower efficiency. Electrically driven pumps are increasingly popular for their higher energy efficiency.
While many studies have optimized standard centrifugal pumps, their results are not directly applicable to the smaller, high-speed automotive coolant pumps with complex flow channels. Recent research focuses on improving the hydraulic performance and heat dissipation of these pumps. This study reshaped the impeller to enhance energy performance and reduce pressure pulsations using CFD analysis. The findings provide valuable insights for optimizing automotive coolant pumps to improve efficiency and reduce energy consumption.
Computation model and research method
Computation model
The automotive coolant pump has design parameters of Qd = 12 m³/h, Hd = 20 m, n = 6000 r/min, and ns = 133. Numerical simulation revealed that the original impeller’s blade outlet angle of 40° caused significant flow diffusion, so it was reduced to 30°.
The original impeller had too many blades, causing hydraulic loss. Reducing the blade number to 6 improved the head to over 20 m. To counteract secondary flows from fewer blades, the wrap angle was increased by 5° for variant A, and by an additional 2° and 4° for variants B and C. Geometrical parameters for the impellers are in Table 1.
Table 1. Main Parameters of the Impellers of Automotive Coolant Pump
Parameter | Description | Original Scheme | Variant A | Variant B | Variant C |
---|---|---|---|---|---|
D1 | Inlet diameter (mm) | 35 | 35 | 35 | 35 |
D2 | Outlet diameter (mm) | 65 | 65 | 65 | 65 |
b2 | Outlet width (mm) | 8 | 8 | 8 | 8 |
β1 | Blade inlet angle (°) | 25 | 25 | 25 | 25 |
β2 | Blade outlet angle (°) | 40 | 30 | 30 | 30 |
ψ | Blade wrap angle (°) | 78 | 83 | 85 | 87 |
Z | Blade number | 8 | 6 | 6 | 6 |
Mesh and independence check
Mesh has a great influence on the accuracy of the numerical simulations and the calculation time. In this work, the meshes within the computation domain were generated using the commercial software ICEM CFD. An unstructured tetrahedral mesh with good fitting ability was used in mesh generation.
To ensure the accuracy of the computation result based on the time saving, five different meshes were selected for each impeller scheme to check the mesh independence. The computation results for the design flow Qd are shown in Figure 2.
As shown in Figure 2, the deviation of the pumping head for each scheme is within an interval of 0.5% when the number of cells is larger than 1.2 × 106. Considering the computation accuracy and time, tetrahedral mesh with a total number of 1,453,619, 1,510,535, 1,490,535, 1,510,535, and 1,470,535 cells were selected for numerical simulation in the original scheme, variant A, variant B, and variant C, respectively.
As an example, the mesh of original impeller domain is shown in Figure 3 with enlarged view for showing the near-wall prism layers. The y+ value was also checked for applying the scalable wall functions. Totally 10 boundary prism layer were set off-wall with the first-layer-height of 0.05 mm and y+ below 10–100.
Numerical computation method
The numerical computations were performed using the commercial software Ansys CFX. The unsteady and incompressible N-S equations were discretized using the finite element volume method. The pressure-velocity coupling was solved using the SIMPLE algorithm. The convergence criteria for all residuals were set to 10−4. The most widely used k-ε standard model was chosen.
Boundary conditions
The inlet boundary condition was set as total pressure (101,325 Pa). The outlet boundary condition was set as mass flow rate. The no-slip wall was applied to all walls except interfaces, which means that the time-averaged and fluctuating velocities in all directions were 0. According to the actual machining accuracy, the wall roughness was set to 0.0125 mm. The standard wall function was applied to the adjacent areas of the walls.
Arrangement of monitoring points
The time step 8.333 × 10−5 s was chosen so that the impeller rotated 3° in each step. To ensure the accuracy of the analysis, the impeller was set to rotate six times, and at the last rotation, the computational results were analyzed. To analyze the pressure pulsation characteristics in the volute, monitoring points were located in the spiral casing, the diffuser area, and the tongue of the volute. The locations of monitoring points P1, P2, P3, P4, P5, and P6 are shown in Figure 4. All monitoring points were arranged at the center of the spiral casing and diffuser width.
Experiment
The energy performance of the automotive coolant pump with different impellers was tested in the closed-circuit measuring station as shown in Figure 5. The working medium was fresh water. The test rig contains the pump, electric motor, piping, electric valve, pressure transmitter, torque meter, and electromagnetic flow meter.
Buy high-quality essays & assignment writing as per particular university, high school or college by Singapore Writers
The precision of flowmeter is ±0.5%, the precision of torque meter is ±0.25%, the precision of high-speed Hall sensor used for speed measurement is ±0.25%, the precision of pressure transmitter is ±0.1%, and the measurement error of the pressure is ±0.25%. As a result, the measurement error of head is 0.27% and the measurement error of efficiency is 0.67%.
Results and analysis of CFD modeling
Performance analysis
The comparison between experimental and computational characteristic curves of the automotive coolant pump with the original impeller is shown in Figure 6. Comparing the results of experiments and computations, the error in the head is less than 2.6% and the maximum efficiency difference is 3.3%. Therefore, the numerical computational method can be used to reliably predict the performance of the pump.
Characteristic curves, composed of computed heads and efficiencies at five flow rates (0.2Qd, 0.4Qd, 0.6Qd, 0.8Qd, 1.0Qd, 1.2Qd, and 1.4Qd) are shown in Figure 7 for both the original and the three new variants.
As shown in Figure 7, the head decreases noticeably for all impeller variants at 0.8Qd flow rate. The best efficiency point is at 1.2Qd due to the increased flow design method. At 1.0Qd, the calculated heads for the original and new variants are 21.5, 20.8, 20.7, and 20.6 m, with efficiencies of 55.5%, 59.6%, 60.3%, and 60.2%, respectively. Variant B has the highest efficiency, 4.8% higher than the original, despite a 0.8 m lower head, still meeting design requirements.
At low flow rates, the head remains constant while efficiency increases. Variant C shows increased friction losses and lower efficiency due to longer blades. Variant B, selected for 3D printing, showed an optimized runner in Figure 8 and was evaluated as per section 3.
The comparison between experimental and computational characteristics and efficiencies of the automotive coolant pump with optimized impeller is shown in Figure 9.
Figure 9 shows that computational results align well with experimental results, with less than a 2% deviation. At the best efficiency point, the experiment yields a head of 19.62 m and efficiency of 61.2%, while at the design point, the head is 20.23 m and efficiency is 60.2%.
This good agreement indicates the reliability of the numerical simulation. The internal flow and pressure pulsations of the original and optimized variants were compared and analyzed using numerical simulation.
Velocity distribution
The relative flow velocity distributions in the impeller for the original and optimized variants at 0.8Qd, 1.0Qd, and 1.2Qd are shown in Figures 10 and 11. Both Figures show the velocity at the center of the channel cross-section.
For the original impeller, large regions with low relative velocity and vortices are present at 0.8Qd and 1.0Qd flow rates (Figure 10). As the flow rate increases, these vortices diminish.
In the optimized variant, at 0.8Qd, some channels show low relative velocity but lack vortices (Figure 11). As the flow rate increases, velocity uniformity improves, explaining the higher efficiency (Figure 6 vs. Figure 8).
The original impeller shows smaller velocity on the suction side due to an excessive blade outlet angle and small wrap angle, causing a wake area. The optimized variant generates axial vortices, balancing the relative velocity.
Absolute velocity distributions for both schemes at 0.8Qd, 1.0Qd, and 1.2Qd are shown in Figures 12 and 13.
Pressure fluctuations
To analyze the pressure pulsations in the volute, the unsteady numerical simulation of the internal flow in pumps with different impellers was performed. For quantification, the pressure fluctuation coefficient is introduced as follows:
where Δp is the difference between the instantaneous pressure and the mean pressure, ρ is the fluid density, and u2 is the circumferential velocity of the impeller outlet.
Time-domain plots of the pressure fluctuations in monitoring points are shown in Figures 16 and 17. The results are shown for one revolution of the impeller and for rate 1.0Qd. The horizontal coordinate θ represents the angle at which the impeller rotates for one cycle, and the longitudinal coordinate Cp is the pressure fluctuation coefficient of the monitoring points computational according to equation (1).